Analysis of failure induced by temperature cycles in composite and eutectic
SnPb flip chip solder joints (Unpublished report)
K. N. Tu
Dept. of Materials Science &
Engineering, UCLA, Los Angeles, CA 90095-1591
I.
Introduction - Microstructure of flip chip solder joints
The composite flip chip solder joint is defined to
consist of a high-Pb solder (say 90Pb10Sn solder) on the Si chip side and a
eutectic SnPb on the substrate side. The composition of the eutectic
SnPb will be around 60Pb40Sn. The substrate is assumed to be BT resin.
In the composite joint, the eutectic SnPb will be deposited or pasted on a
Cu pad on BT to form solder-on-pad (SOP) before it is reflowed to join to
the high-Pb.
Figure 1(a) depicts the cross-section of a flip chip
composite solder joint. We note that in the reflow, the eutectic SnPb
will wet the high-Pb bump and form a coating around the high-Pb. We
assume a layer of solder of thickness h' near the composition of eutectic
SnPb remains.
Figure 1(b) depicts the cross-section of a eutectic SnPb
flip chip solder joint. The main difference between Fig. 1(a) and 1(b)
is that the joint in Fig. 1(b) is a homogeneous eutectic solder joint.
Here we have ignored different intermetallic compound formation in these two
kinds of joints.
To consider physical properties of the solders, for
simplicity, we shall use pure Pb to represent the high-Pb. Actually
the yield stress of 90Pb10Sn should be higher than that of pure Pb. We
also include data of pure Sn for comparison. We find that,
|
Sn |
eu-SnPb |
Pb |
Young's
modulus, GPa |
56 |
35 |
16 |
Yield stress,
MPa |
51 |
28.6 |
38.3 |
Melting
point, oC |
232 |
183 |
327 |
It is important to
note that the eutectic SnPb (the middle column) has the lowest yield stress,
which means that when the applied stress in the composite solder joint is
beyond the yield stress, the eutectic SnPb will deform first.
II. Thermal
stress/strain induced by temperature cycling
When the eutectic SnPb is reflowed to join the high-Pb, the reflow
temperature will be slightly above the melting point of the eutectic, which
is about 183 oC. Because the thermal expansion of Si and BT is
different, it will induce a thermal stress in the packaging. We shall
ignore it here, instead we shall concentrate on the thermal stress in
temperature cycles between 20 oC and 105 oC. The latter is about the
device operation temperature. So
DT = 85
oC. The thermal expansion
coefficient “a" of Si and BT are 2.6 ppm/oC and 25 ppm/oC, respective, so
Da
= 22.4 ppm/ oC. Thus the thermal or shear strain will be
(1)
Now in Figure 2(a), we depict a schematic diagram of a
flip chip. The largest shear strain will occur at the corner solder
bumps at the diagonal direction of the Si chip. If we assume the size
of the Si chip to be 1 cm x 1 cm, we have l = 21/2/2 cm =
0.707 cm, which is the distance of half of the diagonal of the chip,
measuring from the center of the chip to its corner. Substituting the
values of Da , DT, and l into Eq. (1), we obtain ΔDl = 13.5 µm.
We have ignored the tensile strain in the above analysis.
In Figure 2(b), we depict the deformation of an array of
solder joints by the thermal stress. It is known that the electronic
industry has used underfill to redistribute the thermal stress. If the
underfill has low glass transition temperature, it becomes soft at the
device operation temperature, and the thermal stress will be taken up mostly
by the solder joints. The solder joint at the corners will fail first.
III. Failure analysis
To consider failure caused by the thermal stress, if we assume the height of
the solder bump to be h = 100 µm, thus the shear strain is ΔDl/h =
13.5/100 ~ 13 %. We recall that elastic limit is only 0.2 %. Then if
we multiple it by the modulus (Let us assume the Young's modulus and the
shear modulus are not that different) as given in the last section on
Introduction, we shall have the stress, which is much greater than the yield
stress. Thus, the joint will be deformed plastically.
However, in the composite solder joint, when the layer of
eutectic SnPb yields first, its thickness is much less than the total height
of the solder bump. If we assume the thickness of the eutectic SnPb
layer to be h' = 10 µm, the shear strain in it will be
ΔDl/h' =
13.5/10. Clearly the strain in the eutectic SnPb layer (in the composite
solder joint) is about one order of magnitude higher than that in the
homogeneous eutectic SnPb solder joint.
Furthermore, strain energy is given as stress times strain and it will be
proportional to the square of strain, so the strain energy imparted to the
eutectic SnPb by the thermal stress will be about 100 times larger than that
to the eutectic SnPb solder joint.
If we define that due to temperature cycles, the failure occurs when the
accumulated strain energy is beyond a certain threshold value, then fracture
will occur and the joint will fail. We will not discuss the failure
mechanism, e.g., how the crack nucleates and propagates, instead we just
define the energetic criterion of failure as below. When the
accumulated plastic energy is beyond a critical value of Wcrit,
failure occurs.
(2)
where (DW/VDt) is
the plastic strain energy produced per unit temperature cycle per unit
volume of the solder, having a unit of joule/cm3-sec, V is the
volume of the solder in units of cm3,Dt is the period of one
temperature cycle, in units of sec. In each cycle, there will be
elastic deformation as well as plastic deformation. We assume that
when the total plastic energy or work-done to the solder is beyond a
threshold value, it will crack due to excessive work hardening and sever
plastic deformation. Since the plastic energy produced in the
eutectic SnPb layer in the composite joint is about 100 times larger than
that in the homogeneous eutectic SnPb joint, we expect the cycle times needs
to fail the latter will be 100 times longer. But the above model is
ideal, nevertheless it is reasonable to say that it is at the least 10 times
longer. It is worth noting that the size of the chip can change and
the thickness of the eutectic SnPb layer, h', in the composite can change,
yet the overall outcome and reasoning remain the same.
IV.
Other considerations
(a) Stress relaxation
In the above analysis, we have not considered stress relaxation. Since
solder materials have a high homologous temperature at the device operation
temperature, a certain amount of stress relaxation can occur, especially by
creep. In creep, atomic diffusion is driven by a stress gradient.
We shall consider the rate of diffusion in the solder joint first and then
discuss the stress gradient.
If we take lattice diffusivity in eutectic SnPb to be
(3)
where D0 is
pre-exponential factor, which can be taken to be about 0.1 cm2/sec,
ΔH is activation enthalpy of diffusion, which for eutectic SnPb can be taken
to be about 0.8 eV/atom, and kT has the usual meaning of thermal energy. At
105 oC, we obtain D ≈ 10 -12 cm2/sec. In a period of
time of 12 hours, the diffusion distance can be estimated to be about 2 to 5
µm. At room temperature, the diffusion distance will be much smaller. For
creep to reduce stress, the atoms may need to diffuse to the free surface of
the solder joint (because of stress gradient), which has an average distance
of half of the diameter or half of the height of the solder bump, which is
about 50 µm. Thus creep will not be able to relax all the stress and
strain. If atoms diffuse instead to internal surfaces, grain boundaries, or
dislocations, it tends to cause void formation and crack formation and
enhances failure.
(b)
Electromigration
While the high-Pb solder is known to have better
resistance to electromigration, eutectic solder is not, especially when
current crowding occurs at the cathode entrance where the electrons enter
the solder bumps. When the applied current density is above 5 x 103
A/cm2, electromigration occurs rather faster in the eutectic
solder. Whether electromigration will enhance the failure caused by
temperature cycle or power cycle is unclear at the moment. It needs to be
addressed.
(c)
Intermetallic compound formation
The distribution of intermetallic compound (IMC) in the
flip chip solder joint should be investigated to see if it has any effect on
the fracture failure. A very thick IMC will enhance the model of failure
presented in the above.
(d)
Coffin-Manson model of low cycle fatigue failure
The classic model of low cycle fatigue failure in high-Pb
C-4 solder joints (not the composite solder joint) has been investigated by
the model of Coffin-Manson in which a power relation between plastic strain
and number of cycle was given. It will not be reviewed here. But it will
be of interest to see if the model can be applied to the failure observed in
the composite solder joints under a very large strain.
V.
Executive Summary
The composite solder joint has a built-in weakness due to
the thin layer of eutectic SnPb solder in the joint. The eutectic SnPb has
a low yield stress and it will deform first and lead to stress concentration
and to accumulate high plastic strain energy.
The homogeneous eutectic SnPb solder joint tends to have
a uniform composition and much lower plastic deformation so the accumulation
of plastic strain energy per unit volume is lower.
If we define the failure by an energy criterion, the
eutectic SnPb solder joint may have at least ten times longer life-time than
the composite solder joint.
For life-time prediction, the real microstructure of
these two kinds of flip chip solder joint should be studied and actual
failure rate should be measured.
Reference:
K. N. Tu, “Solder joint technology: Materials, properties, and reliability,"
Springer, New York (2007).
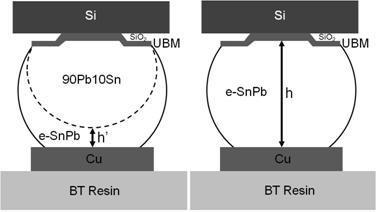
Fig. 1(a) Schematic diagram of the cross-section of a composite high-Pb and
eutectic SnPbflip chip solder joint. (b) A eutectic SnPb flip chip solder
joint.
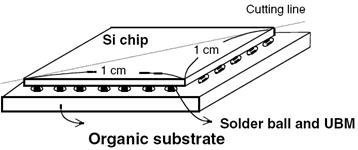
Fig. 2(a) Schematic diagram of a flip chip on a substrate. The diagonal of
the chip is shown.
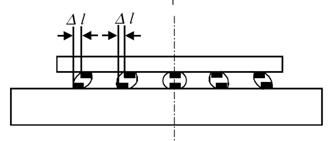
Figure 2(b) Schematic diagram of the cross-section of an array of deformed
solder joints under thermal stress.
|